Sullair provides a fully customised solution that improves air quality, reliability and efficiency to major packaging manufacturer, Visy
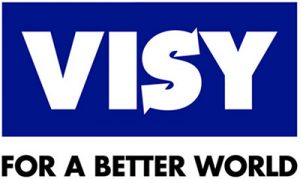
THE BRIEF
Our client is Visy Board, an Australasian packaging manufacturer, with operations in more than 120 sites across the region. In this case, the site in Yatala, Brisbane specialises in the manufacturing of corrugated cardboard products.
Our client:
- Manufactures corrugated cardboard from original materials (recycled fibre and craft paper)
- Prepares the corrugated cardboard to be made into other products
- Provides customised solutions across industry including retail, wholesale, export, and specialist areas such as cold chain, heavy-duty and dangerous goods.
The key part of their manufacturing process involves corrugators – equipment that creates the board corrugations. Cardboard backing is then joined onto the corrugated product. There is a critical need for significant, quality air to run the equipment, to ensure pneumatic components are not at risk of contamination.
The site itself was subject to high temperatures and the existing compressors were experiencing persistent overheating that affected production. Unreliable water was entering the plant and air quality was challenged as a result of both of these factors. There was no standby or back up system in place and emergency hire equipment would be needed in the event of services or unplanned breakdowns.
The overall outcome of these issues was decreased efficiency and reliability, and increased risk, due to the constant overheating of the compressors, the risk of failure of onboard dryers and the absence of redundancy measures in the event of equipment failure.
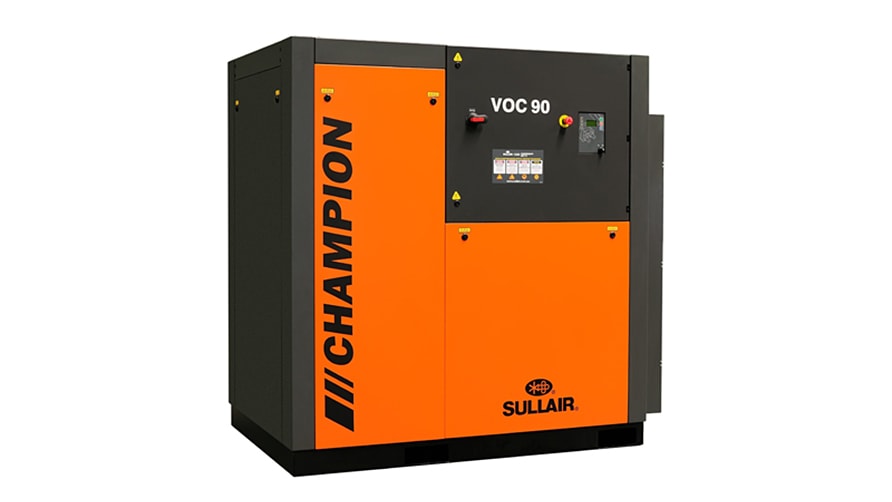
THE SOLUTION
Brent Marshall is Queensland’s Regional Sales Manager for Sullair, and he worked closely with Visy on customising their solution. “In industry, heat is the enemy. In many cases heat can build up within the compressor room, recirculating hot air contributes to machines running hot. Inherent with overheating is instant reliability and air quality issues for the customer, and that’s where we get involved”.
The brief was for an upgrade of existing compressors and dryers, including the provision of capital equipment, install design and full mechanical installation of the new machinery, with piping and by-passes. The installation involved three VOC 90s; one variable speed drive (VSD) and two fixed-speed compressors, along with a total redesign of the compressor layout and the space itself. The project required consultation with both the customer and the installation team and included the addition of a mezzanine floor to accommodate additional air dryers and filtration, as well as maximise the serviceability and health and safety aspects of the installation.
Sullair provided the ducting and consulted with Visy’s engineering and project managers on the overall design layout to ensure the final result was a fully integrated turnkey solution. It also needed to be a ‘hot install’ – in that it was delivered without interruption to Visy’s production schedule.
“When you’re working with companies that have that level of professionalism within their project team and their engineering team, it complements the whole outcome”.
THE RESULT
The outcome is a fully integrated professional installation, with all the necessary equipment included and optimised for the site’s production requirements. Marshall worked closely with Visy Board Yatala’s Maintenance Manager, Grant Marwood on the solution. “The previous situation meant all compressors had to be running to maintain production, so we couldn’t do maintenance during the week. We previously had integral dryers in the compressor units, and the compressors would run hot, which was always problematic”, explains Marwood. “Brent was very knowledgeable and helpful, and we are really happy with the outcomes. Overall, it worked out really nicely and everyone’s quite pleased with the layout and the solution we now have in place.”
Serviceability, safety and energy efficiency have been dramatically improved and a comprehensive backup capability put in place, ensuring the plant can still run at full capacity during service or repairs to any one of the machines. Air quality is now at a premium due to the drying equipment, filtration and bypasses included in the installation. The site can now run 24/7 without the previously experienced complications, and energy efficiency, air quality and environmental expectations are being met.
On reflection, Brent Marshall sees the collaboration on this project as a great story for Sullair and Visy Board. “When you’re working with companies that have that level of professionalism within their project team and their engineering team, it complements the whole outcome”.