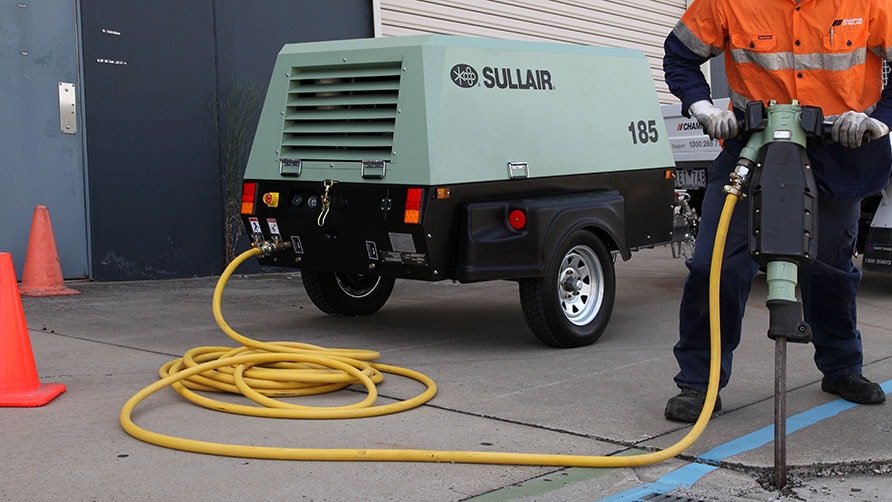
By Nav Sharma
The adage holds true: if you take care of your equipment, it’ll take care of you. To help extend the life of your portable air compressors, it’s important to follow a pre-established maintenance routine to care for your machine. Ignoring this may result in your machine unexpectedly breaking down or an overall shorter lifespan—something no business can afford.
While there are many factors affecting the routine maintenance schedules of portable air compressors – such as climate, operating conditions, the specific machine, and engine manufacturer – there are routine maintenance procedures that apply to nearly all compressors.
Consistent and correctly performed maintenance will ensure the compressor’s performance and extend its operational life.
Following is a set frequency preventative maintenance plan for a 185 cfm portable diesel air compressor. Set frequency maintenance plans can vary based on engine manufacturer, compressor size, climate and day-to-day operating conditions.
Taking on the responsibility of maintaining your equipment is a commitment to its longevity. Completing maintenance will avoid costly downtime, frustrating troubleshooting, and additional costs in the event of equipment failure.
Daily maintenance should include:
- Checking all oil and fluid levels in the engine and compressor
- Adding oil and/or fluids if necessary
- Filling the fuel tank and draining any water from the fuel/water separator
- Checking the dust collectors and cleaning if necessary
- Checking and cleaning the coolers if working in dirty environments
In addition to daily checks and maintenance, the first inspection after 50 hours is important for the machine, which is also a ‘break-in inspection’ to eliminate contaminants from the machine. Please refer to the manufacturer user manuals for proper inspection and maintenance. It is also important to inspect radiators and coolers every 100 hours to ensure the engine and compressors stay at the recommended temperatures. Dirty or clogged up coolers and radiators are the most common reason for a machine to overheat and shut down.
Be sure to also check for compressor oil quality using the provided sight glass. This is especially important in high humidity conditions and when the compressor has been running on idle for a long period of time under moderate temperatures.
The most common wear parts in portable air compressors are filters and engine belts. In addition to air and oil filters, change the engine and compressor oil according to manufacturer recommendations, just as you would on your car. One simple standard practice to follow includes always maintaining a ready stock of replacement parts to avoid downtime and allowing you to complete maintenance in a timely manner.
Some manufacturers like Sullair offer service and maintenance kits at 250, 500 and 2,000-hour intervals to help with maintaining a ready stock of replacement parts and filters necessary for these recommended service intervals. These kits are specifically created with end users in mind to take the guesswork out of maintenance parts. Use the slow times of year to perform these preventative maintenance activities and get your fleet ready for the busy construction season.