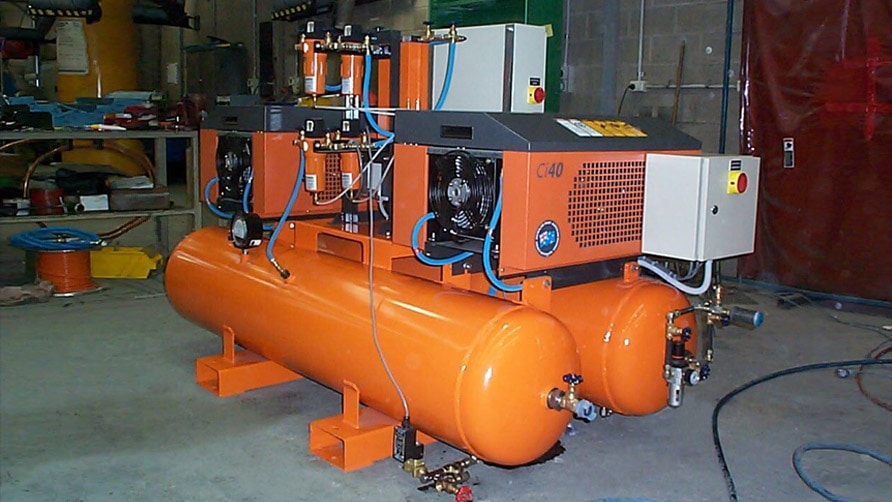
Developments in product design and advancements in technology mean at some point, different elements of a piece of equipment will become redundant. When equipment is designed to last for decades or more, this can become problematic as parts age and repair or replacement becomes necessary.
The Sydney Sullair Australia team were recently approached by a client with a situation like this – degradation of a part that had been in operation for more than 2 decades. With some strategic thinking and a collaborative approach – the help of Fluid Dynamics Melbourne, a long-term partner they were able to customize a solution. The challenge began when Sullair was approached by their client, who has a pumping station on-site, delivering an essential utility to a consumer base. Their issue arose from a small hole in the oil/aftercooler, in a Champion Ci75 duplex compressor unit. On-site the compressed air is used to power pneumatic controls and instrumentation involved in pumping.
The unit was an engineered product, installed on-site in the early 2000s and now decommissioned, with replacement parts unavailable – including the oil/aftercooler. In addition, replacement of the entire unit with the current model CSI was not an option; it was too difficult to remove this particular machine from its current location for repairs to be made off-site, and it couldn’t be taken out of service as it is critical infrastructure.
Sullair Service Business Consultant Brett Dunlop was in charge of the project, along with the Sydney Spares and Service Team and knew they needed to think creatively to develop an alternative solution. Because of the age of the equipment, along with it being designed overseas, there were no blueprints available for the existing parts to design from. In discussion with Sullair’s engineering unit, it was established that the only solution would be to have a new part redesigned and remade from scratch, with an Australian supplier.
The first step towards this was to generate some drawings, so Dunlop reached out to a long term Sullair partner – Fluid Dynamics in Melbourne. “We didn’t have a blueprint or drawing, or an old example that we could manufacture from, and we couldn’t take the one that was on-site, so we were left with no choice but to draw it ourselves”. Fluid Dynamics designs, manufactures, and provides heat exchange solutions, so was perfectly placed to assist Sullair in customising a solution for their client. “We measured the cooler’s exact dimensions – where its mounting brackets were and its physical dimensions and we drew it up on paper,” explains Dunlop. “Fluid Dynamics sent us the unit they designed from those initial drawings and after a little tweaking, it was installed and was the perfect fit. The benefit of the Australian based supplier is that refinements could be made and turned around quickly”.
“We didn’t have a blueprint or drawing, or an old example that we could manufacture from, and we couldn’t take the one that was on-site, so we were left with no choice but to draw it ourselves”
Once the solution was installed, the customer expressed concern that the same issue might arise with the other cooler. The unit is a duplex, so there is a second oil/aftercooler in the other cooler also. With the failed cooler now removed, it could be sent to Fluid Dynamics, giving them an exact model to design from moving forward. Dunlop explains, “Fluid Dynamics used that as the blueprint instead of using the drawings, so the customer holds a brand-new spare in stock now, in the event that the cooler in the second compressor meets the same fate as the first one did.”
The service offering here provided double benefit in that not only was the client’s initial problem solved but a preventative measure was also identified and implemented. The client has the spare in stock and can immediately action the solution in the event of a future failure. They can also order custom designed spares moving forward if either of the replacement coolers have issues. Having a local supplier to collaborate with really enhanced the service delivery on this project. “From an Australian manufacturer’s point of view, it was fantastic – it showed us why we would try and use Australian manufacturers when we can.”
Interested in finding out more?
Interested in finding out more about how the Sullair Australia team can improve your setup? Contact us today.