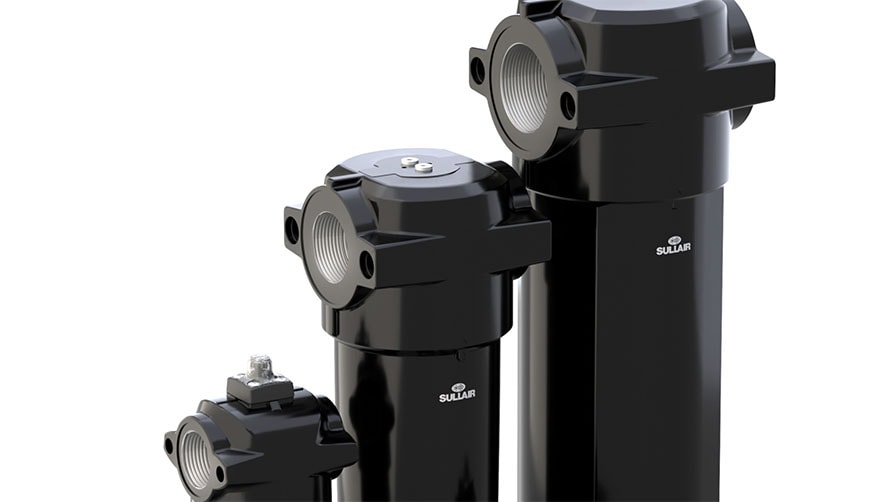
Some may ask why an air compressor needs an air filter? Or does it really matter which air filter you choose? Well, the answer is that it does matter!
You only have one chance to stop contaminants – the number one enemy of rotary screw compressors – from getting into your machine and the type of filter you use will determine how effectively this happens. Contamination causes other problems in a compressed air system, like bearing wear, a reduced air/oil separator life, reduced lubricant life and added costs. The use of inferior filtration accelerates these issues, making the air inlet filter the most important filter in your compressor.
How does your air inlet filter stack up?
Conventional air filters are made of cellulose fibre elements, which often contain less media, reducing filter life and not conforming to OEM dimensions which can then lead to leaks. When opting to use Sullair high-performance air filters you are choosing a product with a unique, proprietary filter media which utilises nanofiber technology. The high-efficiency filter element media is manufactured from borosilicate nano-fibres with a voids-volume of 96% and an external drainage layer. The ultra-fine filtration media contains two layers. In addition to the cellulose media substrate, an extremely fine layer of fibres only 0.2 to 0.3 microns in diameter, capture contaminants less than one micron in size. Rapid accumulation of particles on the filter surface builds a thin, permeable dust-stopping cake, which ensures the highest filtration efficiency by eliminating premature filtration efficiency with very low pressure drop.
Sullair’s SL filter series enhance the compressor’s efficiency and life of the filters, resulting in high quality and cost-effective filtration that outperforms the competition.
Why does filtration media matter?
Where the differences in conventional cellulose media vs. SL filter series media become very apparent is in where the contaminants are captured. SL series filter fibres have submicron diameters and small spaces between the fibres, which result in more contaminants being captured on the surface of the media and lower restriction. Cellulose fibres are larger than SL filter fibres and have larger inter-fibre spaces, causing contaminants to load in the depth of the media. Airflow is then restricted, capacity is lessened, and life is shortened.
With depth loading:
- Openings between fibres become plugged, reducing open area
- Reduced open area causes velocities to increase
- Increased velocities raise pressure and lower compressor efficiency
This contrasts with SL series filters which have higher initial efficiency than conventional media and are 99.99% efficient per ISO-5011. Sullair’s SL series filters last longer than conventional media due to superior surface loading.
Benefits of surface loading:
- Dirt cakes on the surface rather than plugging the internal openings
- When the compressor unloads, the caked dust can separate from the surface web layer
- This process will repeat many times, extending filter life
When selecting filter elements for your compressor, it’s important to look beyond the price tag and to instead consider the long-term costs and repercussions. Choosing an extra efficiency replacement filter, means fewer change intervals, which saves you on both filter costs and maintenance downtime, which no one can afford.
Why is superior filtration important?
Compressed air must be produced to quality in accordance with ISO 8573-1:2001, however the quality of compressed air required will vary depending on the application. The demands for purity and quality are far greater when manufacturing pharmaceutical products or foodstuffs for example, than for the operation of pneumatic tools on a production line. The international standard for compressed air quality provides a simple and clear system which classifies the three main sources of contamination present in all compressed air systems: water, oil and particulate. Sullair Australia aims to always take on an advisory role on the subject of oil injected with filtration vs oil free. Supporting the customer with insights into best practice, whilst assisting them to make choices around the best equipment for their needs is paramount.
As well as the removal of contamination, the economics of using compressed air filters play an important role. Here, the requirement is one of minimising costs and achieving a balance between the compressed air quality being sought and the amount of energy necessary to achieve it.