Sullair Australia provides international green tea company ITO EN with customised oil-free solution
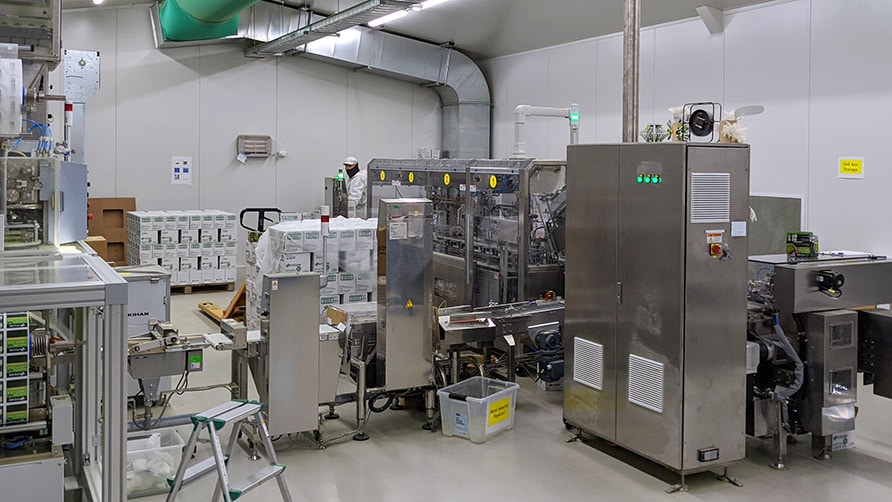
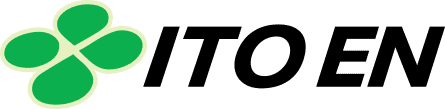
THE BRIEF
Our client, ITO EN Australia, is a subsidiary of the largest green tea manufacturers in Japan, ITO EN Japan. The company has been growing and processing crude green tea in regional Victoria for almost 30 years, for export supply primarily to the parent company.
Our client produces and manufactures green tea products including:
- Single-use teabags
- Matcha+tea blended product
- Blended product packaged tea bags
Recently the decision was made to establish an Australian manufacturing site as the first location outside of Japan. This was a new innovation for our client and their parent company, to sustain and grow their existing business with major Australian supermarket brands.
The brief required that the tea bags be manufactured in a clean room environment, with all of the equipment associated with that manufacturing, producing clean dry air. In addition, a reliable and consistent supply of quality nitrogen was needed. Oil free production was essential to conform to ISO 8573-1:2010, to meet the parent company’s QA standards.
ITO EN Australia’s Manufacturing Coordinator, Rory Brooksbank explains their process. “Our current set up manufactures tea bags out of a mix of refined tea and matcha. It uses a filter material to wrap the teabag, cut it, put it in an envelope, flush it out with nitrogen to keep it fresh, then go on to be collated into 20 and put into a box.” Compressors were needed at multiple stages of the production cycle and Sullair was engaged to custom fit a solution.
THE SOLUTION
We proposed a combination compressor and N2generation package. This included the Hitachi Oil Free Air SRL22ME5A Scroll Compressor, which is third party certified to Class Zero as 100% oil free. The air treatment included a 1,000L air receiver, air filtration and a refrigerated dryer (+3 degrees C pressure dew point). The zero class air passes through an N2 generator to deliver 99.5% N2purity that was supported by a 500L N2receiver, N2filtration and a desiccant dryer (-40 degrees C pressure dew point).
The solution was fit-for-purpose because:
- The oil free solution mitigates the risk of any air system failure, by eliminating reliance on a traditional oil lubricant compressor and its necessary filtration measures.
- Oil free ensures there’s 0% oil used in the production cycle, removing the risk entirely of air being contaminated.
- The pneumatics that drive all the machinery are driven by the Sullair compressors – from the packaging and sterilisation equipment in the clean production room, to outside in the N2 generator.
- Application of nitrogen to the product is an essential stage of manufacturing. Clean, high quality inert nitrogen is injected into the tea bag, creating an oxygen free environment so no bacterial growth can occur. The customised N2 solution made the need for (and high risk of) nitrogen bottle purchasing and storage redundant.
- The QA from the parent company required production that adhered to a global standard – by producing to that standard, the product is market ready for continued supply to the parent company and broader export purposes.
THE RESULT
Our close collaboration with our client from the early stages of the project, enabled us to develop a sophisticated understanding of their needs. By comparing and contrasting those local needs, with the operations of the parent company in Japan, we were able to discuss the available technologies and end up with a final solution that was right for them. The combination of oil free compressor solutions and on-site nitrogen production allowed them to establish a purpose-built production facility, using custom fit equipment from Sullair.
Our client is now processing orders for contracts with major Australian supermarket brands and demand has increased considerably as a result, with product being manufactured at the rate of 70 tea bags per minute. As a food and beverage manufacturer, the oil free assurance is the most valuable component of the solution. “The Quality Assurance requirements designated by our parent company specify that zero trace of oil exists in the product”, explains Brooksbank. “Each day production sends samples to the parent company and we are yet to see a single trace of oil in the production system.”