Emergency installation provides a fully operational turnkey solution
THE BRIEF
Our client is a global company that manufactures and supplies consumables for the mining industry. Prior to initially meeting with Sullair, they had been considering upgrading their old equipment in response to increased compressed air supply demand due to growth.
This decision was escalated after a competitor’s compressor installed inside the client’s factory caught fire, damaging the internals of the compressor and its connecting pipework. It also damaged an adjacent compressor control panel and pipework, making it redundant. They required a solution that replaced what they had, increased their capacity and got them up and running as quickly as possible.
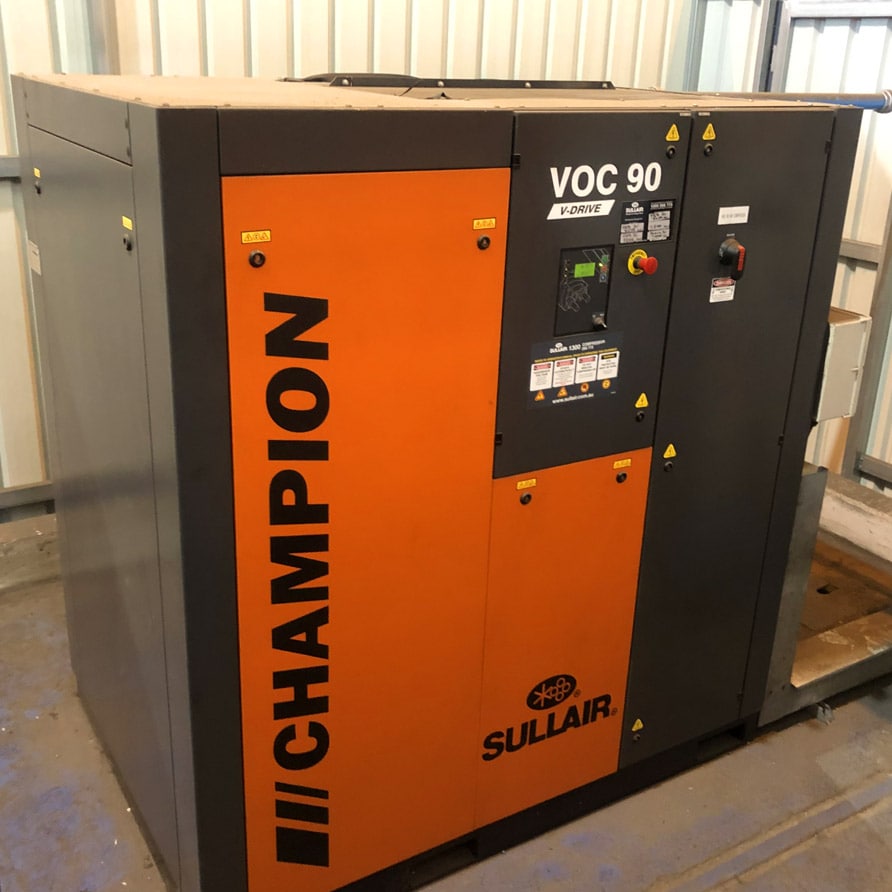
THE SOLUTION
A turnkey solution had to be quickly developed and installed, to minimise downtime and reduce operational expenditure, as the client was hiring compressors temporarily in the interim. This meant higher diesel fuel costs and poorer quality air being pumped into the facility.
Sullair quoted the supply of two new compressors, an upgraded dryer, new connecting pipework and commissioning of the system. Because operations needed to be maintained during the install, we installed each unit as it became available. The installation was completed in three stages.
Stage 1: installation and commission of a VOC 90 VSD compressor, with pipework laid in preparation of the second compressor, VOC110.
We had one VOC 90 VSD compressor in stock in Melbourne, so once all the capital was agreed upon, we supplied the one that was in stock, and got it shipped and installed within a month. We also prepared for stage 2 by replacing the fire damaged pipework and installing the new pipework for the second compressor. This meant that once it arrived, it could simply be plumbed in without interrupting existing operations.
Stage 2: installation and commission of the VOC110 compressor.
The second compressor turned up about a month later and we were able to quickly and seamlessly install it, commission it and get it up and running alongside the VOC 90 VSD.
Stage 3: disconnection of the old refrigerant dryer, installation of new and commissioning of the complete system.
With the upgrade of the compressors, the dryer also needed upgrading, so when the refrigerant dryer came, that was the last piece of the puzzle. We replaced the old dryer with the new one and ran all of the necessary new pipework providing a fully operational turnkey solution.
“Sullair definitely exceeded our expectations. Things run so much better than they ever did, and we have no air problems now whatsoever.”
THE RESULT
The solution was fully installed and operational by May 2020 and since then, all machines have been running without fault, and according to our client, providing a better solution than what was previously in place. “Previously when we did blasting with the old compressors, we didn’t have quite enough air at the four extremities of our 7-hectare site and now we can more than keep up with the demand,” explains our client’s Maintenance Leading Hand.