Nitrogen generator solutions for the mining industry
THE BRIEF
Finding innovative ways to do things better on large mine sites, and in ways that considerably reduce risk is paramount. This means identifying how to solve problems in ways that reduce maintenance and operational costs, while implementing solutions that create a safer environment for everyone on site.
One area where change is being made is around tyre inflation on haul trucks. Traditionally these huge tyres have been inflated using air that is drawn from the atmosphere (comprised of around 78% nitrogen, 21% oxygen and some water vapour) and delivered into the chamber of the tyre at high pressure via an air compressor. There are inherent risks with this however: oxygen is extremely flammable; oxygen molecules are prone to leaking from fully inflated tyres requiring regular tyre reinflation; and water content in compressed air contributes to corrosion of rims, valves and other internal parts. All of these events can cause, at best temporary periods of downtime and at worst, weeks of shutdown if lives are lost.
Of these stoppages, hot tyre events are probably the most concerning. Every year mine sites across the country endure multiple stoppages from hot tyre events. As well as causing considerable disruption and resulting in huge cost blow outs with every incident, they also present a considerable threat to life for everyone on site. Hot tyre events occur when tyres are impacted by excess or unusual heat, from the outside environment (such as high usage volume in extreme environmental temperatures, or lightning strikes) or through heat generated within the tyre chamber itself (from friction or separation of internal components). With oxygen involved, the outcome in any event is combustion, fire, or explosion – all of which present an alarming risk of injury or death. In Australia this is particularly significant with mines located in some of the most remote and therefore hottest and harshest environments in the country.
Removing oxygen from the equation has become the obvious conclusion and many sites are switching to nitrogen as an alternative solution for on-site tyre inflation. Though a much safer and more efficient solution, nitrogen supply has been considerably costly and problematic until recently, with bottled nitrogen the most common source of delivery to sites. The impracticalities of this are widely known – the bottles are cumbersome to transport, deliver and install, and the sheer distances involved in this transportation result in a far from ideal carbon footprint.
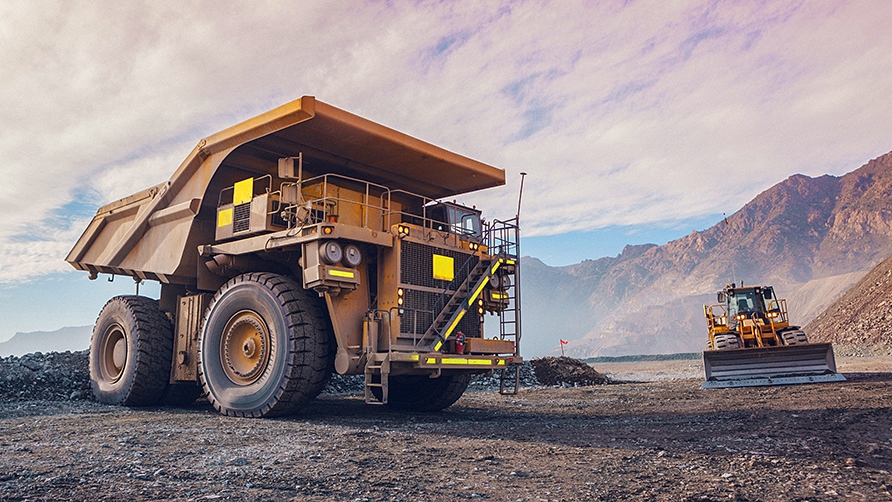
THE SOLUTION
An innovative alternative to the constant laborious import of bottled nitrogen to mining locations, is on-site nitrogen generation. Sullair now has the capacity to bring together its advanced compressed air technology, with nitrogen generator technology to provide turn-key nitrogen gas systems. The addition of a simple, low capital cost item in the form of a nitrogen generator, will deliver sites with nitrogen in abundance and oxygen too if needed.
The convenience, flexibility and improved safety considerations that the nitrogen generator solutions have to offer is undeniable. Sullair’s nitrogen generators filter and separate the nitrogen gas from the oxygen gas, then the gear is mounted on a skid and can be dropped into position at a mine site. With nitrogen drawn from the surrounding air, it is free and available in abundance. Sullair’s generators can provide the customer with the specific concentration of nitrogen they need, with ranges between 95.0% to 99.999%. Those additional costs associated with traditional supply (via bottles, cylinders, mini tanks and so on) are eliminated. Without the added expense of externally produced nitrogen, as well as its delivery, storage, and removal costs, all the customer is paying for is the initial capital outlay and their ongoing running costs. Sullair’s nitrogen packages include skid design, assembly, and delivery as well as containerised systems, giving the client full flexibility.
Sullair’s nitrogen packages include skid design, assembly and delivery as well as containerised systems, giving the client full flexibility.
“We do nitrogen skids all the time, but the containerised solution is ideal for all the mining companies – we simply drop it on to the site where they want it and plug it in ready for operation.”
THE RESULT
The switch from oxygen to nitrogen delivers a number of benefits. Not only does efficiency improve, with more up time and less downtime, the safety considerations are truly remarkable. Because nitrogen is a dry, inert, non-reactive gas, all of the issues previously outlined are largely resolved. The hazards of internal fires and explosions are eliminated without the presence of oxygen; the removal of condensate and water vapour prevents opportunities for corrosion and oxidation; nitrogen has better inflation qualities than oxygen, ensuring tyres are fully inflated to accurate pressures and incidents of critical leakage and rapid deflation are reduced (if not eliminated altogether); the tyres themselves last longer, with wear and tear minimised as the nitrogen makes them more resistant to temperature extremes; and of course, the hefty carbon footprint evolving from nitrogen bottle delivery across the country is dramatically reduced.
Major OEM tyre manufacturers including Michelin, Bridgestone and Caterpillar have all recommended the use of nitrogen gas for tyre inflation, for many of the reasons already detailed – reduced fire risk, better inflation quality and pressure, and reduced damage to tyres through oxidation, corrosion and degradation.
Interested in finding out more?
To learn more about Sullair’s nitrogen generator solutions, call Sullair today on 1300 266 773 or contact us here.