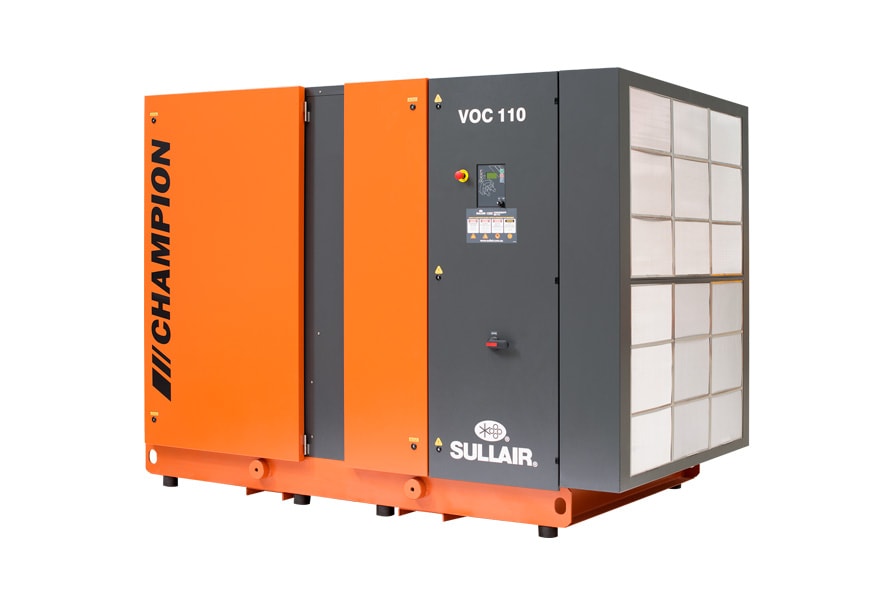
In industries where compressed air is an essential driver of operations, reliable compressors that provide consistent supply are critical. The decisions around equipment repair or replacement are usually made in a considered and strategic way – how reliable is the current machinery, and when will the running costs exceed the replacement costs?
Information around the age of the equipment, records of scheduled servicing, and forecasted production needs are accessible and on hand. Robust decisions around best performance outcomes are made, with a commitment to hefty capital expenditure outlays if required. It’s a best-case scenario situation. Then the COVID-19 pandemic took hold and the worst-case scenario happened.
Across industry, the impacts were many and varied: while some businesses shutdown completely overnight, losing all revenue, staff and hope; others scrambled to manage production schedules and continuity under new restrictions, that were both vague and definitive, all at once. The COVID-19 environment made equipment management that much more challenging, especially where CapEx purchases were concerned.
Those in charge of operations found themselves having to review the realities around sustaining production, while growing market uncertainty chipped away at their confidence – or even capacity – to invest in capital purchases. Timing became everything and those with a solid understanding of their equipment, where it was at in its life span and its condition in any given month, certainly had the competitive advantage to make informed choices.
This approach calls to mind a familiar concept across industry: the bathtub curve is a measure of reliability across the lifespan of, in this case, a piece of equipment. For those managing high end equipment, critical to production schedules during the COVID-19 shutdown, its relevancy became starkly obvious.
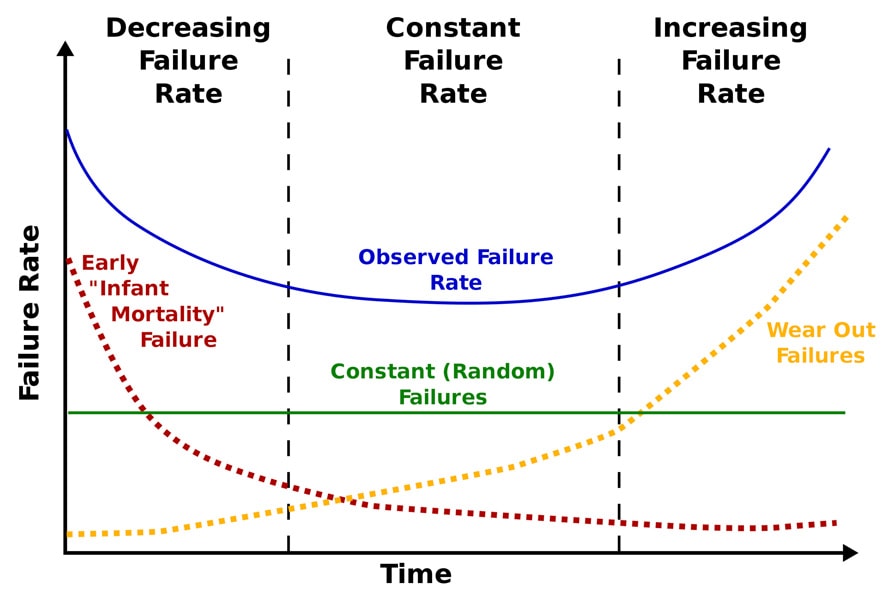
The ‘bathtub curve’ hazard function (blue, upper solid line) is a combination of a decreasing hazard of early failure (red dotted line) and an increasing hazard of wear-out failure (yellow dotted line), plus some constant hazard of random failure (green, lower solid line).
Image and caption source: Wikipedia
The bathtub curve deals with 3 stages within a product’s life cycle. The first stage deals with early issues stemming from the build or workmanship of new equipment, shortly after purchase – the curve slopes upwards. These ‘infantile failures’ are often covered under warranty and easily resolved via tech support, service, or replacement parts. Once infantile failures are dealt with, quality equipment should seamlessly transition into the next stage of non-events: the curve flattens out (like the base of a bathtub) and the machine functions to its capacity for much of its working lifetime, without incident.
Head of Aftermarket at Sullair, Steve Cowburn explains what this looks like from a service team’s perspective. “When techs do regular service, there are about 11 or 12 factors they measure – temperature, pressures, vibrations and so on. If these things measure normal at every service, the bottom of the bathtub curve is sustained. As soon as one of those factors changes consistently across services, we know there’s an issue developing”. This is where the third ‘end of life’ stage kicks in and has been where the decisions around repair or replacement of equipment became more complex, for many businesses during the shutdown.
In a business as usual environment, scheduled servicing, knowing the equipment life span and budgeted equipment expenditure are ideally considered, forecasted and planned for.
Additionally, the ongoing costs of retaining an ageing compressor must be factored into decision making. Compressed air systems account for up to 10% of all of Australia’s industrial electricity use, and the air compressor is often the largest single source of energy consumption in a manufacturing facility1.
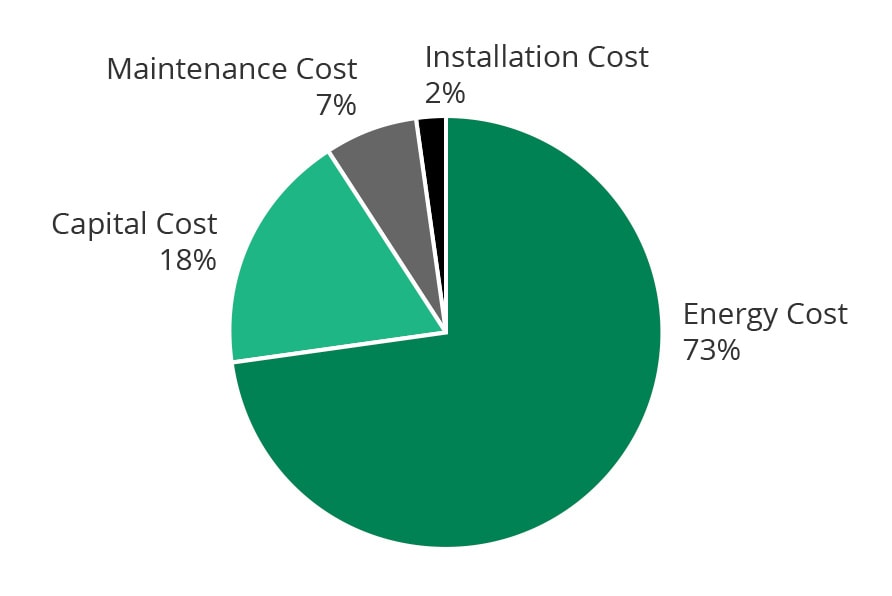
Typical cost breakdown for an air compressor over its operating life.
Source: “My compressor has failed! Repair or Replace?” Steve Cowburn
“The choice will almost always be to repair if the cost difference between the two is wide. The closer a repair cost gets to the replacement cost, the more likely a customer will be to replace.” But nobody’s costings factored in a global pandemic, so for many, the timing of end of life equipment issues couldn’t have been worse.
All equipment has a manufacturer-determined life cycle, calculated in hours and clearly stated in product manuals. If an air compressor has an effective working life of 80,000 working hours, that might translate into a 10-year lifespan for 24 hour a day, year-round usage, or a 20-year life span for half of that. If a compressor is close to, or at the end of life stage, decisions around whether to repair or replace become more critical. “Not everyone’s running 24/7 for 365 days a year,” explains Cowburn. “If the manual states a service is needed at 60,000 hours then any potential issues can be picked up well within the machine’s life span and not at end of life, when it might be too late.”
Having a clear sense of the bathtub curve with regard to the equipment being managed is imperative to predicting how long repairs can extend the life of the equipment for, and when a replacement will be required and CapEx spending needs to be factored into the budget. Unsurprisingly, businesses that had made scheduled servicing of compressors a key priority have been able to transition more seamlessly through the challenges. For them service became a key risk mitigation tool.
A business’s compressor dependency varies according to its size and its ongoing compressed air needs. Smaller operations might have more flexibility to juggle jobs whilst a replacement part is ordered, delivered and installed; while larger operations usually have complex backup systems in place, that kick in, in the event of machinery faults or failure. The more mission critical air supply is the more likely you are to have a backup supply. How a business manages its compressor function depends on the criticality of it to that business’ operations. The more critical the equipment, the more scrutinised these decisions become. Compressed air that goes down can be a huge liability with losses in the millions if just one day of production is impacted.
Decisions around equipment management are complex, across all industries, now more than ever. A conscientious approach to making these decisions should always involve a thorough analysis of the costs involved, the pros and cons (See table below) and the critical operational requirements. A healthy dose of expertise never goes astray either. The COVID-19 environment has created an unprecedented situation. Sullair has prioritised their service delivery to focus on the provision of expertise that guides and supports customers to a viable and customised solution.
REPAIR
PROS
- Cheaper to repair than replace
- As spare parts are readily available the compressor will be producing air again much sooner
- Since the machine is existing, your staff would be familiar with its operation and no further training would be required
- No changes to the reticulation system required
CONS
- If the machine is old or done many operational hours, or if the service and maintenance of the machine has not been kept up to date, the machine may experience further failures
REPLACE
PROS
- The peace of mind of knowing you have an all new machine that should give many hours of trouble-free operation
- Modern machines have newer technology which should result in reduced energy costs (which is the major overall cost in operating a compressor)
CONS
- Costs are higher than repair
- It takes longer to procure and install than to repair
- New equipment may mean additional training for your staff
- If you carry spare parts for the existing machine these may not be compatible with the new machine
- Your reticulation system may need modification to accept the new machine
- Peripheral plant (dryers, chillers…) may be incompatible with the new machine and also require replacement
Summary: pros and Cons of repairing and replacing an air compressor.
Source: My compressor has failed! Repair or Replace? Steve Cowburn
- My compressor has failed! Repair or Replace? Steve Cowburn