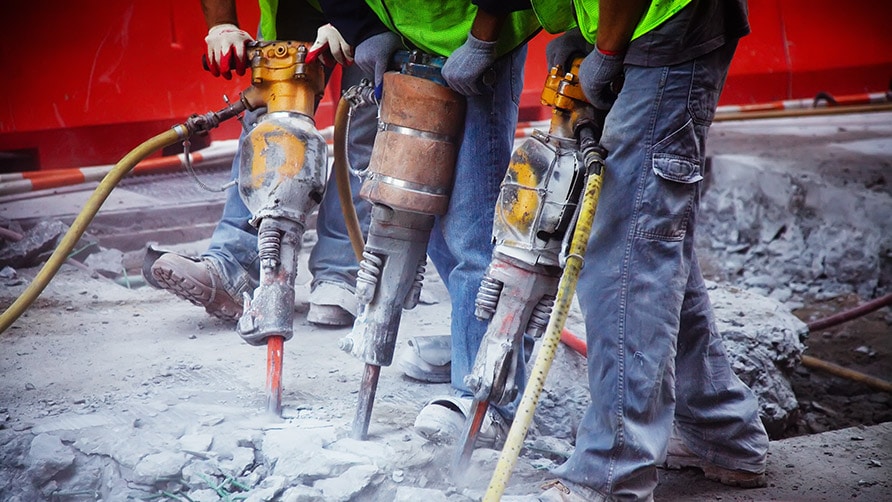
Compressed air is an essential industry, considered just as important as the other major utilities – electricity, water, gas or Internet – in terms of need.
Given they are so essential, why is it we know so little about them? Much like televisions, cars, aircraft and the Internet – some of us may have a rough idea how they work, but if quizzed on specifics, how many of us could really be clear on the detail? Whether your knowledge is excellent, rusty or non-existent, we’ve gone back to basics to get everyone up to speed on the simple but essential basics of air compressors.
What are air compressors?
Compressed air stores potential energy, which is created by an air compressor. The mechanism of action involves air being pumped into an air receiver vessel as stored energy. This can be done in a range of ways – for example via a reciprocating piston or a rotary screw. As the stored compressed air returns back to atmospheric pressure, the energy powers the tools or equipment the compressor is connected to.
The smallest and most accessible example of an air compressor is the humble bike pump, but compressors come in numerous shapes, sizes and capacities – like the ones that are bigger than a human and fitted to turbine engines on planes. Compressors can be mobile, fit for purpose and engineered into other equipment, or fixed in a custom-designed permanent space for large scale industrial use.
Are there different kinds of compressors?
There are different types of compressors and selection comes down to a few key factors which include the quantity and quality of the air that’s needed and how efficient the power consumption will be, based on the length of time it will be used for (both per day and over its lifetime). The two most common types of compressors are reciprocating compressors, and rotary screw compressors.
Reciprocating compressors are piston-driven, with the air decreasing in volume as the pressure increases with the piston being driven at force into a cylinder. These can be oil injected or oil free, depending on the application they’re required for. These are commonly used in small, general purpose operations such as workshops, small scale commercial operations, or handheld equipment for applications that need high pressure, but low flow and need an intermittent supply.
Rotary screw compressors contain two helix shaped screws that mesh with each other, squeezing the air to the discharge port, reducing its volume and increasing its pressure before delivering it to the application point of use. These can also be oil injected or oil free but have a broader range of applications, most of which require specific pressure and flow capacity and often a continuous supply.
Oil injected or oil free?
Compressors that are oil injected tend to be more economical to run and are the most commonly used in the field. They are reliable, resilient and have long life cycles of 25 years or more. However, there are also numerous applications where oil free compressors are essential. More often than not the oil free status applies to manufacturing, with food and beverage and pharmaceutical production as the key industries requiring oil free compressors in their processes. Both industries develop ingestible products so the risk of contamination by oil in the production process must be avoided at all costs. Other examples include industries where contamination would impact on the quality of the product for example grinding prescription lenses, printing, or packaging manufacturing.
What are air compressors used for?
Everything. Every single day, we encounter multiple things in our daily life, that exist in some way because of compressors. Across industry they are an essential piece of equipment that is fundamental to operations – from construction to agriculture, energy to manufacturing, mining to aviation and more. If it needs to be heated, cooled, ventilated, inflated, dug, sealed, moved, cleared, opened, closed … the list goes on. From the smallest application to the largest – taking the wheel nuts off a tyre at the garage, then pumping the tyre with air; powering the tiny torturous drill the dentists uses on our teeth; conveying freshly made polystyrene cups via a tube from one warehouse to another; packing sliced bread or carrots into plastic bags for supermarkets, right up to sterilisation units in major hospitals, dragline operations in open cut mines and engineered solutions for major mining and construction sites; if it needs air pressure to drive or power it, a compressor will reveal itself at some point.
How do I choose the right compressor for our needs?
You can find out more about selection, installation, and maintenance of compressors in our post The ‘how to’ of air compressors.
Sullair’s sales team and technicians are trained to deeply explore the unique needs of our clients. A collaborative approach between your team and ours ensures a comprehensive understanding of the function and application you need. Our focus is on designing fit for purpose solutions that deliver the most suitable product with the right pressure, air flow and quality to meet your requirements today and beyond. Talk to one of our specialist advisors to find out more.