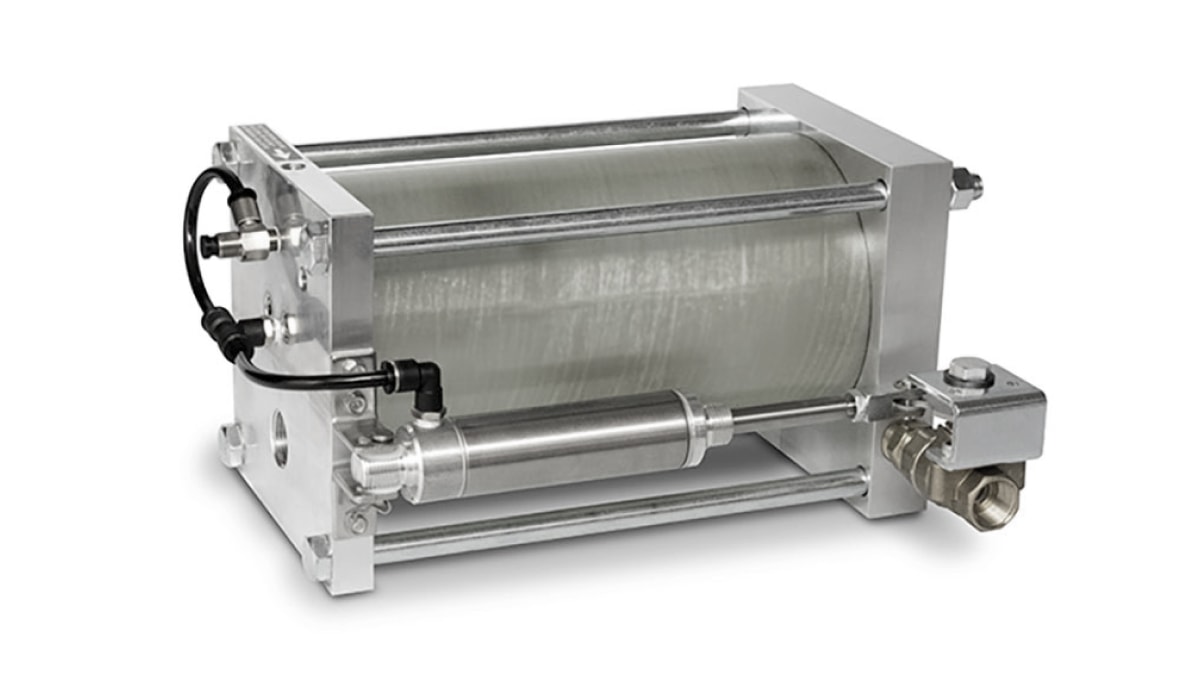
By Kyle Treble and Trevor Hicklin, Hitachi Global Air Power
Condensate is always present in a compressed air system, but it’s also a byproduct that needs to be removed. The presence or build-up of any kind of moisture internally can significantly impact your equipment.
Condensate that isn’t dealt with can create issues in air tool function, impact the quality and efficiency of production, and even result in downtime because major repairs or service needs to happen. Air leaks are costly – inoperable or poorly installed condensate drains can cause a build-up of condensate in the system air receivers, which in turn causes a reduction in storage capacity. That reduction in the system means more cycling of the compressors from load to offload, causing additional wear and tear on your compressor’s bearing.
There are many drain options out there – manual drains, float drains, or solenoid-operated drains – but the benefits of choosing a zero air loss condensate drain are hard to dispute. First, let’s unpack the basics.
What is a zero loss condensate drain?
Zero loss drains are an essential inclusion to your compressed air installation to reliably remove unwanted water, chemicals, or other moisture in the air from your compressed air system. Zero loss drains only open when liquid is present and do not allow compressed air to escape the system. This is an important feature, delivering a functional solution as well as energy savings – don’t forget that compressed air costs money!
Why do you need a zero loss condensate drain?
The zero loss drain is critical to removing condensate. In all industries, the buildup of moisture in the system can create rust and cause corrosion, and when the corrosion is released, it can cause damage to downstream equipment.
Other issues can also occur around moisture stored in a food and beverage installation. Harmful bacteria can develop and the growth rate can be significant in this warm, damp and oxygenated environment. This can be dangerous if there is potential for contact with the product, even contact that’s made through an undetected internal leak of the manufacturing equipment. A zero air loss drain can also ensure moisture is eliminated from the packaging of medications in the pharmaceutical industry as another example of its application.
What are the advantages of choosing a zero loss condensate drain?
Distinguishing features of a zero loss drain compared to other types of drains is the 1/2″ discharge port, a clear vessel to allow visual identification of operation, and ease of installation. It’s also available in pneumatic control, reducing the need for electrical supply.
A zero air loss condensate drain ensures you won’t lose any air pressure while removing moisture because it uniquely retains the air as it works. This is different from manual drains’ function, where operators are required to open the valves to discharge condensate manually. This requires constant attention and leads to excess air loss because the air escapes when the valve is left open to drain the condensate. Lost compressed air is lost money! In addition, as the pressure blows out, you lose pressure and then have to build that pressure back up – meaning your compressor will have to work harder than it really needs to.
This issue is eliminated when choosing a zero loss condensate drain, as it automatically drains the condensate. In addition, when a minimum level of condensate is reached, the valve closes before compressed air can escape.
What kind of savings can I realise?
Some customers shy away from zero loss drains because of a higher upfront cost. However, they often don’t realise the payback is typically returned within 6 – 12 months. Ultimately, your savings would depend on the cost to run the machine, how much air you’re losing and the number of drain valves in your facility.
Our zero loss drain range puts the dollars back in your pocket, with a potential return on investment in as little as one month! A fully serviceable drain means the requirement to replace a complete drain due to a single component failure no longer exists. With its 1/2″ discharge port, our zero loss drains will release debris that would block most other drains in the field without a single puff of air.
The table below gives some estimated annual use costs for different drain types.
This chart illustrates the estimated annual cost of using different drains. The annual cost of using a zero loss drain, is $0.
Zero loss drains are the top choice for reliably removing condensate and preventing the loss and waste of compressed air. Compressed air is one of the most expensive sources of energy in a plant, so who wouldn’t want to reduce the amount of lost air?
Interested in finding out more?
To learn more, call us today on 1300 266 773 or contact us here.