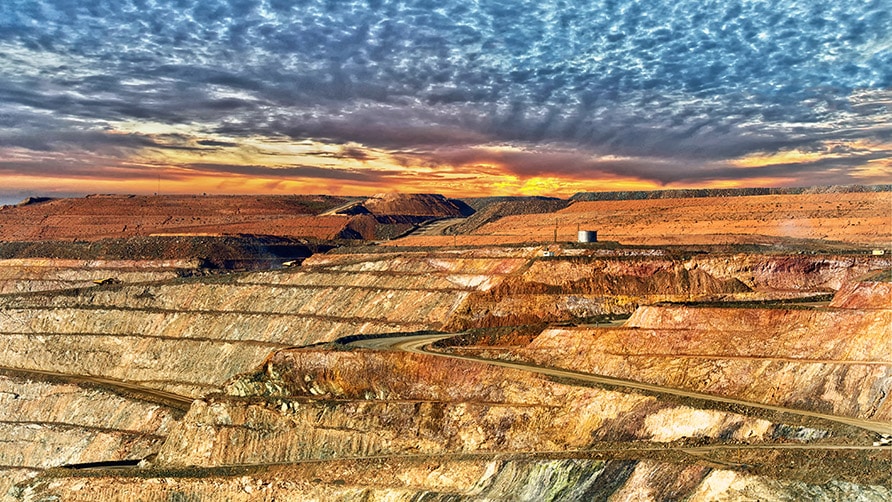
The customised engineering of unique compressor packages has become an essential service for many of Australia’s biggest companies, particularly in the mining sector.
A couple of decades ago, Sullair Australia was the market leader in engineered solutions. “The mining industry boom caved in between 2013 to 2014 and has only really been coming back in the last few years,” explains Denver Alvis, Sullair Australia’s Engineered Solutions Manager. “All are seeing varying degrees of success, but recently the pipeline has been looking really strong as these mining clients are taking on new business.” As a result of this, Sullair has recently made the pivotal decision to get back into the engineered solutions game, with Denver Alvis as National Manager of the Engineered Solutions Division.
“When you look at these engineered solutions projects, they’re quite high value for the customer,” explains Alvis. “Instead of just selling a loose compressor, we build an engineered steel or galvanised skid, mount the compressor, mount the drives, mount the receiver on top, put a roof on it, do all the plumbing, piping and electrical work.” This packaged approach to customisation has multiple benefits. “It’s an integrated system on a single skid – you can just pick it up, put it on the back of a truck, the truck goes out to the mine site, it gets dropped into position and is ready to go.” With many mine sites thousands of kilometres away from a metropolitan centre, the costs involved in getting teams on-site to customise a similar solution are huge – the criticality of Sullair’s offering cannot be underestimated. “It’s far easier and much more economical for us to do it in Melbourne as a turnkey solution and then deliver it, ready for them to plug and play,” explains Alvis.
This repositioning has been possible due to a number of factors, one of which is the excellent reputation of Sullair’s sub-brand, Champion compressors. Denver Alvis and his peers, who’ve spent many years in the industry, know well how highly regarded the Champion brand has been for decades. Sullair’s Champion compressors are designed in Australia, for the harshest of Australian conditions, a reality that cannot be delivered by the competition. Given the demands of the work and the essential need for high-quality, reliable and energy-efficient delivery of compressed air, it’s no wonder some of Australia’s biggest mining companies are so keenly utilising engineered solutions through Sullair. “Champion compressors are unique in that they’re designed in Australia, by Australian engineers, to meet the local mining requirements and have been for over 40 years,” says Alvis.
“Our machines are specifically designed to meet the harsh, hot and dusty environment where these mine sites are located. They’re the only compressor in the world, built from the ground up to be then rated to operate at 50°C.”
In addition to the tough performance credentials of Sullair’s Champion compressors, there are other components to their engineered solutions offering that set Sullair apart from their competitors. Engineered solutions cover not only compressed air but also N2 generators, chiller systems, dryers, blower packages and filtration systems. A feature of the compressors that makes them particularly unique – and therefore coveted in areas such as northern Western Australia and remote parts of the NT – is the heavy-duty cyclonic intake filtration feature, performing the essential role of preventing particles from entering the compressor in dusty conditions.
Importantly though, is the unique and extremely valuable Sullair air-end VOC technology. Alvis is particularly passionate about this advance for the company. “No other compressor in the world has this feature, it’s an energy-saving feature where the VOC makes it 30 to 35% more efficient than comparable fixed speed compressors on part load.” It does this by – as the name suggests – varying its displacement and hence output, through the action of the spiral valve, causing the opening and closing of internal ports within the air-end. The VOC technology enables the length of the compression chamber to be automatically varied, ensuring the output matches the demand more precisely. The VOC technology creates a constant supply of pressure because of the simple and highly reliable spiral valve. Optimal efficiency is maintained with an up to 30-35% power reduction achievable. By controlling the output based on demand, the air-end can run at 50% capacity up to 100% capacity as required. The outcome of course is a more efficient use of energy – especially when contrasted against comparable compressors from Sullair’s direct competitors. In most cases, competitor machines will run either at zero capacity (unloading), or 100% capacity (whether this output is required or not). That it is to say, the compressor is either loading or unloading. The energy used in this ‘all or nothing’ approach is huge – the loading and unloading function of the compressor (in excess of the requirements), results in a less efficient outcome overall. When running multiple machines for many hours, day in and day out, the energy costs certainly add up, so the VOC technology offers huge savings.
Given the outstanding benefits and efficiencies available in Sullair’s engineered solutions, Alvis says it will be great news to many that the company is soon expanding their Melbourne warehouse footprint, with packaging partners being added in NSW, Queensland and Western Australia. “We’re thrilled to be setting up in Perth in particular, because if you look at our engineered solutions locations, 70% of what we’re doing is in the WA mine sites. Clients have flown to Melbourne previously to do the Factory Acceptance Test, or they send an inspector in the final stage. We put everything together, it’s all wired up then we press go so they can see the whole system operating. We run it for several hours and when everyone’s happy, it gets the green light, then we ship it to site. At their end, all they have to do is wire up the electrics to the skid and plumb the air pipes.” Taking the distance out of that scenario represents even further energy and cost efficiencies to their company.
Currently across Australia, Sullair has hundreds of engineered solutions in place with their customers, with a large majority of those in the Pilbara, supported by three permanent on-site technicians. Given the innovation behind Sullair’s new engineered solutions offering, it’s unsurprising that some of the biggest resource customers in the region and Australia consider Sullair one of their preferred suppliers.
The combination of the rugged, Australian-designed Champion compressors with their unique and world-leading, energy-efficient VOC technology, and the 50 deg C. ambient temperature rating, elevates Sullair Engineered Solutions Division into a prime position to support our customers in Australia and the wider region. Sullair, as a Hitachi Group company, is one of the largest designers and manufacturers of compressors globally.