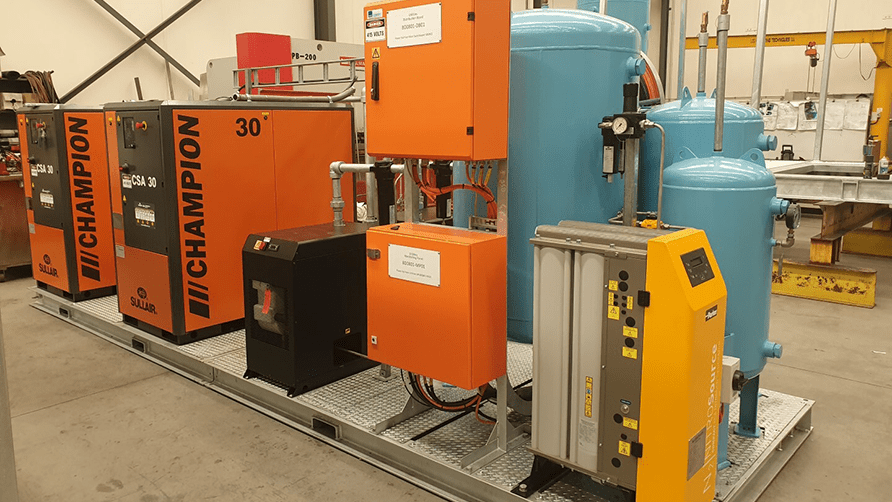
Industry is constantly striving to evolve, but somehow the speed of evolution surpasses our ability to implement new solutions. If you need to revisit how you’re currently sustaining a supply of high quality, uninterrupted nitrogen, you’re in the right place, because we’ve pulled together (almost) everything you need to know about nitrogen generation.
Sticking with the status quo maintains a state of familiarity and comfort, however traditional nitrogen gas supply methods do have an end-of-life date – especially when efficiency, safety, and cost effectiveness are of paramount importance.
How is nitrogen made and what is it used for?
Nitrogen is a colourless, odourless, and tasteless gas that is abundant in the atmosphere making up 78% of the air we breathe. Atmospheric air is drawn into an air compressor, then shunted through a nitrogen gas generator, where trace gases are removed. Nitrogen is isolated during this process, to be delivered directly to a storage vessel and then transported to the end user (external generation – usually by gas companies), or delivered from the nitrogen generator directly into the relevant application the generator is connected to (on site generation).
Nitrogen is most commonly used in the food and beverage, chemical, pharmaceutical, aviation, oil and gas, and electronics industries. In the food industry, it’s often the key line of defence against spoilage and quality reduction. Replacement of oxygen with nitrogen in the production, packaging, and storing of food and beverage products increases product shelf life, appearance, and taste. This is particularly important with fresh food and wine products for example where flavour, aroma and even nutritional content can be significantly impacted by oxidation. When the air space in sealed food products is replaced with nitrogen gas, aerobic bacteria can no longer survive. The product quality is retained, and it will stay fresher and last longer.
It has a significant application in the mining industry also, with major OEM tyre manufacturers including Michelin, Bridgestone and Caterpillar all recommending the use of nitrogen gas for tyre inflation on large vehicles and equipment. Nitrogen is known to have better inflation properties than oxygen and does not suffer the leakage and deflation issues that oxygen does. Removal of oxygen from the inflation process also reduces corrosion and oxidation, general wear-and-tear, and largely eliminates incidents of fires and explosions.
What are the key issues to understand about nitrogen supply?
Traditionally, nitrogen generation and supply has been in the hands of bulk suppliers, who then package it and distribute it to end users in refillable gas cylinders, mini tanks, or bulk storage tanks. This has become an increasingly impractical, costly, and problematic solution over the years. Transportation, installation, and delivery of pre-packaged nitrogen cylinders is extremely cumbersome and generates a large carbon footprint.
The safety issues of externally procured nitrogen are significant as the often-convoluted external supply chain increases the chance of oxygen leakage. Not only is oxygen extremely flammable, but it also creates moisture which can contribute to corrosion of parts, reducing their life span. Nitrogen is often ‘subbed in’ to fill a space dominated by oxygen (by way of replacement) which has considerable safety issues associated with it. Nitrogen is clean, dry, and has a low dew point (<-50°C) making it much safer and more stable than oxygen. Across many industries, oxygen removal will not only prevent the risk of oxidation, and bacteriological growth, it will most importantly mean the risk of fires or explosions is reduced or eliminated.
As a result, companies like Sullair have been offering alternative technologies in the form of nitrogen generation packages that can be used on site. Given the disruption that occurs (production downtimes or worse shutdowns) when gas supply is interrupted or contaminated, these solutions empower end users to be in control of their own gas supply. Nitrogen generated on site offers an uninterrupted supply of high-quality nitrogen and as a result, on site nitrogen generation packages also enable them to have a safer, more efficient, and much more cost-effective solution in place.
How does on site nitrogen generation work?
Sullair offers two key technologies available for producing nitrogen – Hollow Fibre Membrane generators and Pressure Swing Adsorption (PSA) generators. Sullair’s nitrogen generators can provide the customer with whatever concentration of nitrogen they need, from 95.0% to 99.999%. The choice of generator will depend on the required ‘remaining oxygen concentration’ for the specific application. Applications that require HFM generators usually require 5% to 2% maximum remaining oxygen concentration, while applications requiring 1% or less are better suited to PSA generators.
Sullair’s nitrogen generators have a modular design allowing for flexible adaptations to a wide range of environments and applications. Packages include skid design, assembly, and delivery with all-inclusive installation, commissioning, and ongoing service care. The customer’s main expenses will be the initial outlay, and the ongoing running costs. Capital payback from on-site nitrogen generation solutions is typically achievable within 1 to 2 years. Additional costs usually associated with externally sourced nitrogen – unit cost, cylinder rental, delivery, storage, and removal are eliminated. You can learn more about the benefits of nitrogen generation here.
You can find more information, including technical specifications, about Sullair’s nitrogen generators on our website. Alternatively, you can contact your local branch.