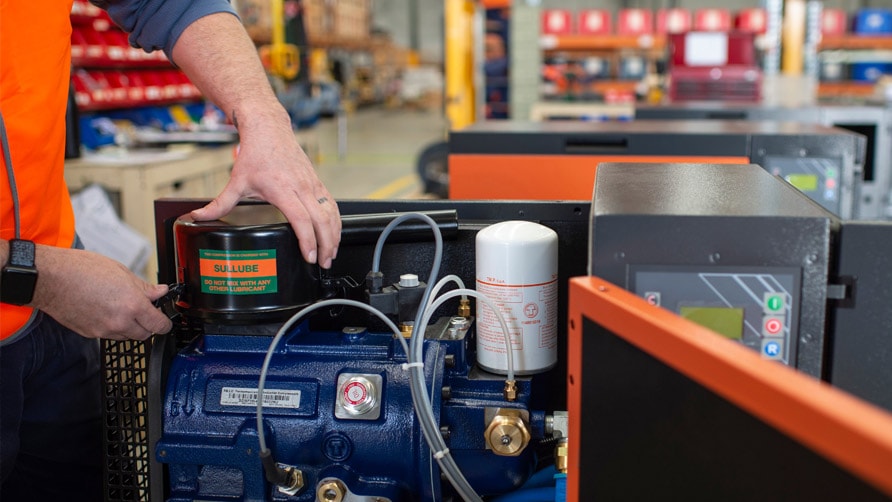
Understanding the basics of air compressors is important but knowing exactly which compressor to choose for your specific requirements is essential.
The first question to consider when choosing a compressor system is what quality of air is needed for the application it will be used for. Discussions should be had around a range of factors. For example, will filtration be required to get the air to the required standard? Does the air need to be in line with quality conforming to class zero? Once the air has been compressed, it is then transferred into an air receiver which stores the high-pressure air and reduces the cycling frequency. An air receiver also serves to remove moisture and is recommended in most installations. Does the air need to be dried further? In which case a dryer will need to be added to the package to remove moisture from the air. All these components should be carefully selected to deliver the required function, but also to work seamlessly together to produce the desired result safely, reliably and efficiently.
Compressor selection
Generally, the selection of the compressor should be based on both the quality and the quantity of air required. Machine choice will then be made around power consumption and energy efficiency to ensure operating costs are maintained in line with existing budgets.
There are a few different types of compressors, so depending on the market segment you’re dealing with, the machine itself should be fit for purpose, with the load cycle determining the machine choice to some extent. Important things to consider are how often is the compressor used? Is it running constantly or intermittently? If it runs consistently over long periods of time, what equipment is going to deliver the most energy efficient solution? If a machine is only going to be used intermittently – for example once a week – a customer may choose a reciprocating compressor, preferring a reduction in capital costs while compromising on running costs; whereas if the same usage is applied day in day out, a rotary screw compressor would be the better choice.
Contrary to popular belief, size does matter. A large compressor for a small job is just as problematic as a small compressor for a large job. An underperforming compressor may generate excess condensate through inefficient heating processes, reducing it’s capacity more quickly over time; while an overworked compressor won’t produce enough air, making it inefficient for the application in question. The life cycle of the compressor will be impacted in both instances, so efficiency is not just about day to day operations, but also efficiency of equipment over the long term.
Compressor installation
After selection of the right compressor comes installation. Ventilation space, piping design and most importantly safety, are all important considerations when it comes to installation – from a single compressor unit, right up to a fully customized turnkey solution. The positioning of the equipment within the facility must take into consideration environmental issues such as quality of the source air coming into the unit, as well as the recirculation of exhaust air. Some components such as air receivers may need to be outside of the building, so equipment inside needs to be strategically positioned to ensure safe and efficient connection between the components. For ongoing maintenance, equipment should be installed in a way that makes it easily and safely accessible to technicians and of course the same applies for day-to-day operations.
Compressor maintenance
When it comes to compressor maintenance there are two options – preventative maintenance and responsive maintenance. The latter is necessary when equipment is malfunctioning, broken or failing and can be extremely costly if it halts production – or worse – initiates a shutdown for more extensive repairs. A proactive approach however, in most cases will prevent costly incidents of unplanned downtime. It will also enable you to get the full life out of your compressor. A preventative maintenance plan ensures even the highest quality products, designed and purpose built for their application and environment are given the utmost care and attention, throughout their life cycle. This type of maintenance needs to be targeted, with trained technicians and support from service to service, to ensure no breakdowns occur between services.
These are all important points to discuss with your production team and your sales agent. Refining these details will enable you to choose from the specific range of compressors best suited to your requirements. Sullair’s sales team and technicians are trained to deeply explore the unique needs of our clients. A collaborative approach between your team and ours ensures a comprehensive understanding of the function required for the specific application. Our focus is on designing fit-for-purpose solutions that deliver the most suitable product with the right pressure, air flow and quality to meet your requirements today and beyond. Talk to one of our specialist advisors to find out more.